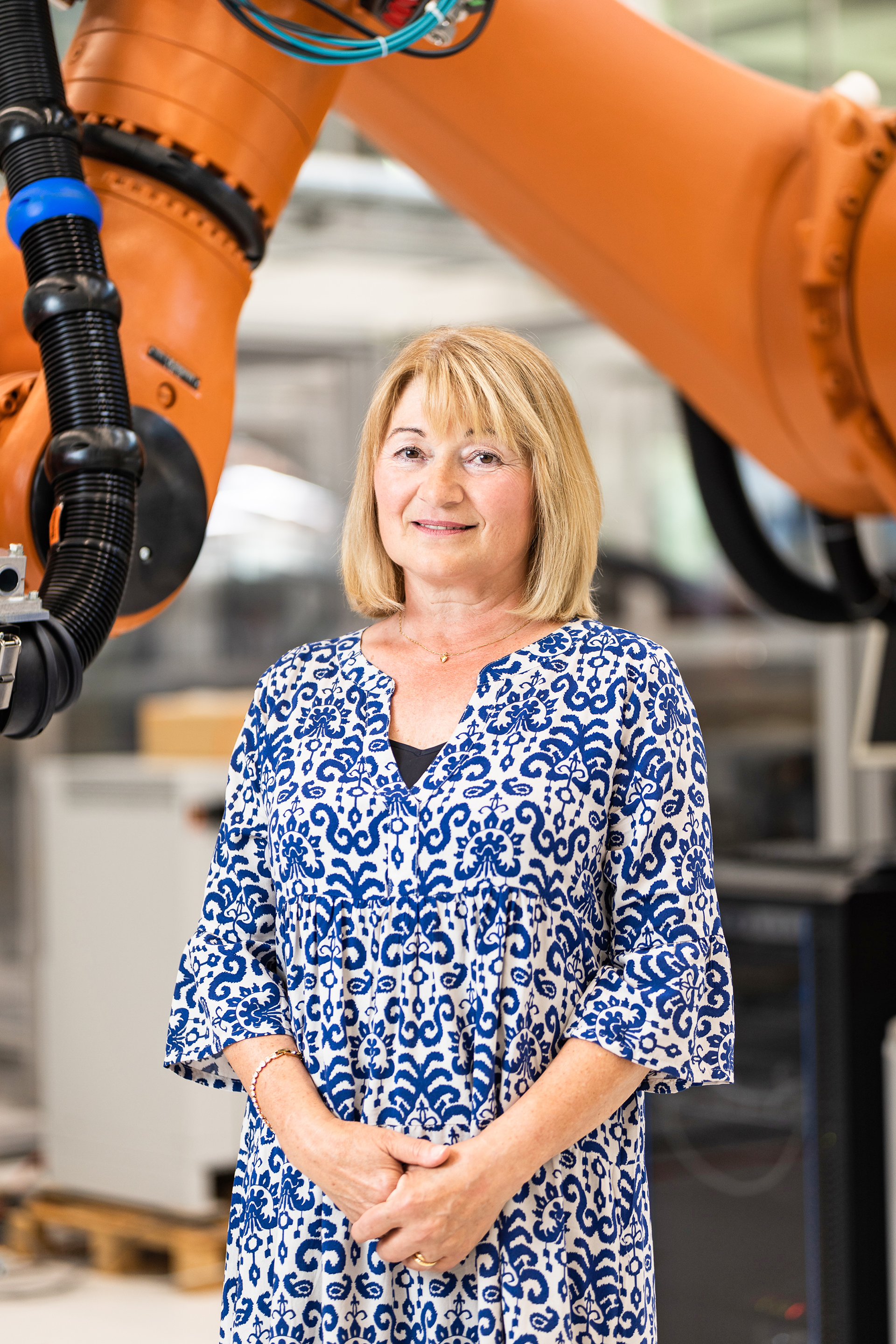
In modernen Fabriken können kleine Störungen eine Kaskade von Problemen verursachen. Im Projekt »I4Produktion« entwickelt das Fraunhofer IAO gemeinsam mit Partnern aus der Wirtschaft eine Künstliche Intelligenz, die helfen soll, Produktionsabläufe stets effizient zu gestalten.
Eigentlich ist die Aufgabe, die der AGV (Autonomous Ground Vehicle), ein lasergeführter, fahrerloser Gabelstapler, jetzt übernehmen soll, einfach: ein Bauteil für einen Pkw zur nächsten Produktionsstufe bringen. Doch etwas ist anders an diesem Tag. Der Korridor mitten durch die Halle, durch die der Wagen normalerweise fährt, ist blockiert. Dort sind Absperrbänder gespannt, weil hier Bauarbeiten stattfinden.
»Der Kleine weiß ganz genau, dass er einen anderen Weg nehmen muss«, sagt Professorin Carmen Constantinescu, die jede Bewegung des Roboters genau beobachtet – allerdings nicht in der Realität. Sie schaut sich eine Computersimulation auf einem Monitor an. Und in diesem Moment sieht sie, dass der AGV einen anderen Weg einschlägt, er wählt einen Korridor am Rand der Fabrikhalle, um seine Fracht ans Ziel zu bringen. Bei dieser Entscheidung musste kein Mensch helfen. Der Roboter wird durch eine Künstliche Intelligenz (KI) gesteuert.
Ein Forschungscampus für Wirtschaft und Wissenschaft
Genau daran arbeitet die Ingenieurin Carmen Constantinescu mit ihrem Projekt »I4Produktion« für das Fraunhofer IAO. Der Projektname steht für: »Alle Augen auf die Produktion«. Das Ziel ist eine smarteFabrik, die mithilfe von umfangreichen Daten die Produktion fehlerfrei und mit optimaler Kapazität aufrechterhält. In so einer Fabrik erkennen Kameras und Sensoren blockierte Wege, dann leitet das System Transportroboter um. In dieser Fabrik bringen die Transportroboter einer Mitarbeiterin, die kurz davor ist, ein schweres Bauteil zu bewegen, ein Exoskelett, das beim Heben schwerer Lasten unterstützt. So eine Fabrik passt Arbeitspläne automatisch und in Echtzeit an, um Ausfälle durch Krankmeldungen auszugleichen.
»Wir arbeiten an einer resilienten Fabrik«, sagt Prof. Dr. Carmen Constantinescu. Menschen gelten als resilient, wenn sie schwierige Lebenssituationen ohne dauerhafte Beeinträchtigung überstehen. Eine resiliente Fabrik soll am Optimum produzieren, auch wenn Störungen auftauchen.